The past 10 years has seen a significant shift in the amount of new overdrive 5 & 6-speed transmissions being retro-fitted into older cars and trucks. There is just something nostalgic about rowing gears in a classic muscle car that can’t be satisfied by any other means. Pair that up with the new fuel injected engines available today and you have a combination of modern power with classic styling that you just can’t replicate in a new car. But… before we get too geeked up and rush to replace that tired 3 or 4-speed, we need to be sure we take the proper precautions for a trouble free installation and a good long life for your new transmission.
In the past, if you’ve had a car with a factory 4-speed and you needed to change out to another 4-speed, it was an easy swap over as nothing really needed to be changed. Today in many of the builds we see a change in flywheels, clutches, and types of bellhousings to accommodate these newer transmissions. True, many of the new 5-speeds will bolt into the same bellhousings that those 4-speeds came out of, but if the bellhousing has been removed from the engine it will be important to re-align the bellhousing upon installation.
Before installing your new transmission, it is very important to make sure that your bellhousing is properly aligned with the centerline of the crankshaft. You will also want to take the time to ensure that the flywheel is flat against the crankshaft as well. In this guide, we will cover the processes of aligning all the components to ensure a great experience once all the new parts are installed. The last thing anyone wants is to spend a few thousand on a transmission package only to have problems a few hundred miles down the road.

A bellhousing that is not concentric or parallel with the crankshaft centerline will give the transmission poor shift quality as it is putting excessive side load on the input shaft. You may also experience accelerated clutch wear, engagement problems, accelerated input shaft bearing wear, pilot bushing noise/excessive wear, and an overall dissatisfying experience with the performance of your new transmission. Even if you do a dry fit and everything “slides right together” doesn’t guarantee a proper alignment. The only way to know for sure is to take the time to do these measurements.
Checking the bellhousing alignment can be a tedious task, especially if the engine is still in the car, but it is essential for proper operation. If anything, do the alignment to ensure that if you should have a warranty claim that it will not be immediately dismissed due to improper alignment. (Trust us, it is immediately evident when a transmission wasn’t aligned properly, this will almost always void any warranty claims)
Measurement Quick Reference
Standard Automotive Bellhousing Alignment Specifications:
Concentric: +/-.005” or .010” TIR Parallel: +/-.001” or .002” TIR
Hi-Performance 7,500+ RPM Bellhousing Alignment Specifications:
Concentric: +/-.0025” or .005” TIR Parallel: +/-.0005” or .001” TIR
Flywheel runout .001” to .005” Max (less is always better)
Before you get started it is always helpful to go ahead and ensure a smooth, clean mating surface for all the components. This means metal to metal contact may be the only way to get the measurements you need. Normally you will be able to get by with making sure the block surface and crank flange is rust/paint free and the dowel pins are clean of any debris. There shouldn’t be any nicks or burrs either. In some rare cases, it may be necessary to clear the paint from the bellhousing if there is significant build up. A bellhousing that is quite a bit out of parallel will need to be shimmed regardless.

Flywheel Runout
The first part of a successful install will be to ensure that your flywheel is parallel with the crank shaft flange. This will give you a good foundation to work from when checking the bell housing alignment.
- First be sure the crank flange is clean/rust free. Bolt up the flywheel and torque the bolts to spec.
- Set up your dial indicator perpendicular to the flywheel clutch surface. This can be done by attaching the magnetic base to the oil pan or engine block.
- Be sure to zero out your indicator and mark your starting point. Then slowly crank the engine by hand for one full revolution (360*) to be sure you come back to a zero reading at your starting point. Do this one more revolution to ensure repeatability and that your dial indicator is mounted securely.
- Once you have your starting point established make another rotation and note for any low (negative) readings. If you have any negative readings, mark that spot and that will be your new zero starting point. If you have no negative readings move on to the next step.
- Now that you have verified your zero-starting point make a couple revolutions and note any high spots. You should end up with no more than .005” TIR. As always, the lower number the better.
- If you end up with more than .005” TIR there is a possibility that your flywheel is warped, damaged, or needs to be resurfaced. At this point it may also be necessary to check the crank flange for run out as well to be sure it does not have any damage.
- Once you have your flywheel runout within spec you are ready to move onto checking the bell housing alignment.
** NOTE: If you are working with an aluminum flywheel you may need to remove it for the bellhousing alignment. This will allow you to mount the magnetic dial indicator base to the crankshaft flange for a more solid connection.

Checking Bellhousing Concentric Alignment
There are different procedures to follow depending on your transmission. The TKO 5-speed and Magnum 6-speed utilize two different styles of bellhousing. The TKO 5-speed can be dial indicated on the bellhousing opening, whereas, currently, to do a proper alignment for the Magnum 6-speed, the front cover of the transmission will have to be removed and bolted to the bellhousing so that the input shaft bearing race can be utilized for measuring. From there the measuring procedures are the same.
TKO 5-speed owners: There is one more item to be checked before you get started: the front bearing retainer on the transmission. It is the outer diameter of this retainer that determines the concentric placement of the transmission on the bellhousing, not the transmission bolts. Therefore, it is important that the bearing retainer be the right one to work with the bellhousing being used. The retainer should be a snug fit in to the opening in the bellhousing. If it is not, another retainer of the proper diameter must be found (most manufacturers have produced bearing retainers in a number of different diameters). Another alternative is to use a spacer bushing in the bellhousing opening.
- After ensuring you have a clean/rust free mating surface. Secure the bellhousing to the engine block and torque all bellhousing to engine bolts to specification. If using a scattershield, make sure the block plate is installed. Magnum 6-speed owners will also bolt on your front cover at this point, but be sure to attach your magnetic dial indicator base to the flywheel before the front cover goes on.
Note: The stock dowel pins must protrude out past the block plate/scattershield and locate on the cylindrical part of the dowel pins, not the tapered end. If the scattershield is resting on the tapered end, it will cause an inaccurate alignment reading. If necessary, tap the stock dowel pins rearward, just enough for the tapered end to protrude through the scattershield
- With the engine cylinder #1 on TDC (Top Dead Center), install the dial indicator base on the flywheel. Adjusting the plunger to contact the inside edge of the bellhousing transmission register hole at 12:00, or if aligning for a Magnum 6-speed, you will use the input shaft bearing race to measure from. If needed, removing two flywheel bolts 180* apart for the dial indicator to sit flush on the flywheel is OK.
Note: The magnetic based indicator does not need to be on the exact center of the flywheel. TDC/12:00 dial indicator setup will allow better communication with your helper to stop at TDC/12:00 for the repeatability checks.
Aluminum Flywheel Users: you will need to remove your flywheel for the alignment check. The magnetic base indicator will not attach to an aluminum flywheel.
- With the dial indicator on (0) zero and mounted securely at 12:00, your helper can rotate the crankshaft 360* slowly. Your job is to note the dial indicator reading, you are looking for the most (-) negative number on the dial indicator as it rotates the 360*. When your helper rotating the crankshaft stops on TDC, your dial indicator should read (0) zero at 12:00. If you read (0) zero, then you have verified your dial indicator is mounted securely. Do another crankshaft rotation to double check your dial indicator still reads (0) zero at 12:00.
- With the dial indicator still secured at 12:00; note the most (-) negative number of the dial indicator during your next 360* rotations. Once you are certain where the most (-) negative number is, mark the bellhousing. This most (-) negative number will be your new dial indicator (0) zero location.
Note: The most (-) negative number dial indicator reading can be at any location within your 360* rotation.
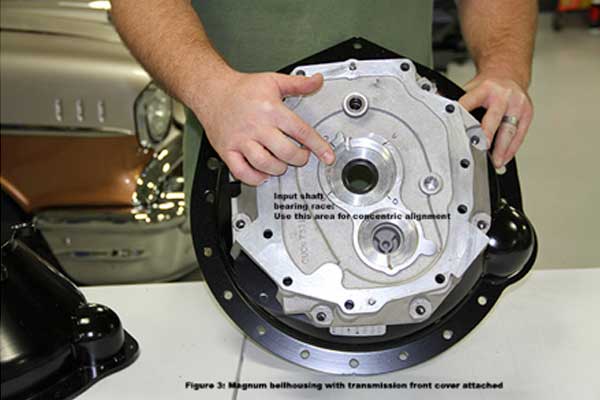
Bellhousing Mis-Alignment Exercise Example:
If you have determined your most (-) negative number is at 8:00; rotate the crankshaft until the dial indicator is at 8:00 and (0) zero the dial indicator. As your helper rotates the crankshaft from the new 8:00 (0) zero location, your most (+) positive number should be roughly at 2:00 or 180* from the new 8:00 (0) zero location. The TIR (Total Indicator Reading) of the dial indicator needle from 8:00 to 2:00 is your bellhousing register hole to crankshaft centerline misalignment. If the TIR was +.028” on the dial indicator, you divide .028” / 2 = .014”. and .014” would be the needed offset dowel pin to correct your bellhousing concentric misalignment. The .014” offset dowel pins would also point towards 2:00 to correct the bellhousing mis-alignment.
Checking Bellhousing Parallel Alignment
• With the engine on TDC and the dial indicator base still mounted on the flywheel, adjust the plunger to contact the front face of the bellhousing at 12:00.
Note: The bellhousing front face is the contact area your transmission mounts to. You can add a piece of packaging tape to cover the clutch fork pivotball threaded hole. The packaging tape will also allow the plunger to glide over the hole opening.
• With the dial indicator on (0) zero and mounted securely at 12:00, your helper can rotate the crankshaft 360* slowly. As before, your job is to note the dial indicator reading, you are looking for the most (-) negative number on the dial indicator as it rotates the 360*. When your helper rotating the crankshaft stops on TDC, your dial indicator should read (0) zero at 12:00. If you read (0) zero, then you have verified your dial indicator is mounted securely. Do another crankshaft rotation to double check your dial indicator still reads (0) zero at 12:00.
• Your most (-) negative number will require shims between the engine block and bellhousing to correct the parallel alignment.
Bellhousing Alignment Helpful Hints
Do the concentric bellhousing alignment check, but do not make any offset dowel pin corrections at this time.
Do a parallel alignment check and if needed, shim the bellhousing to achieve parallel alignment specs.
Note: Aligning a bellhousing to within parallel specs will change the bellhousing concentric reading.
Do another concentric alignment check and use the correct offset alignment dowel pins to achieve your concentric alignment specifications.
TIR = “Total Indicator Runout”. The needed Offset Dowels to achieve the concentric alignment specs will always be ½ of your TIR. TIR of .028” will use a .014” offset dowel pin to correct the concentric misalignment.
Total Indicator Reading | ½ of TIR | Use Offset Dowels |
---|---|---|
.012” to .020” | .006” to .010” | .007” |
.022” to .034” | .011” to .017” | .014” |
.036” to .052” | .018” to .026” | .021” |
The better a bellhousing is indexed and dial indicated to the crankshaft, the smoother performance, higher RPM shifts, and transmission longevity you will experience.
If your bellhousing requires offset dowel pins (contact your local speed shop and see if the dowel pins are available in the proper offset for your block). Before installing the offset pins we recommend to drill and tap a small hole into the side of each, dowel pin hole (in the block) so that a small Allen-head set screw can be used to lock the offset pins in the proper orientation after alignment is completed. When installed, the offset dowel pins can be adjusted with a screw-driver to obtain the proper alignment. In some cases, the dowel pins must be polished with a strip of emery cloth to permit them to be rotated in the dowel pin holes with a screw-driver. Adjustment with these offset pins can be tedious and time consuming so be patient. After this is completed, tighten all bellhousing bolts and recheck the alignment one more time. If everything is okay, the bellhousing portion of the job is done and you are ready to move forward with the rest of the installation.
There is a lot of information here to digest, but do not let it overwhelm you or make you nervous. The majority of the time your bellhousing will fall within spec and you will be good to go, but there are some instances where it will be necessary to utilize the offset dowel pins and it is important to take the necessary steps to get the proper alignment. This extra time spent setting everything up properly will save you many hours and dollars later should yours be out of the acceptable tolerance range. We stress the importance of this because of the problems we’ve seen over the years and we want to try and save you the time and expense of correcting this problem at a later time when the damage has already been done.